An experienced Repair and Restoration technician speaks about Gibson’s use of PLEK machines and human expertise
To provide a more consistent fretting experience from one guitar to the next, Gibson uses PLEK® technology. Developed by Gerd Anke of A+D Guitarrentechnologie GmbH in Berlin, Germany, PLEK is a computer-controlled system that provides the finishing touch to a guitar’s frets with incredible consistency. PLEK (both Pro and Station) uses a rotary cutter to remove material, and this leaves behind a reasonably smooth surface that has a radiused crown, but there is still quite a bit of hand work needed to get them to Gibson’s standard for fret dressing.
While PLEK may measure the radius at each fret, it only displays this data as the radius at the 1st, 12th, and last fret (whether it is 19, 20, 21, 22, etc.). Plek measures and reports the radius during the fret-cutting process on the “Virtual Fret Dress” screen, as it is as critical to fret leveling as it is to fretboard planing. The system is so intelligent that it can tell the operator if the guitar requires a truss rod tweak before applying the PLEK process.
PLEK provides a post-scan image to the user that shows the actual height of each fret (a line in red) with a second line to indicate the ideal target height (in green). The same post-scan screen(s) provide a view of the measured fingerboard surface (in gray) and a second line in blue to show the ideal relief.
Sample below:
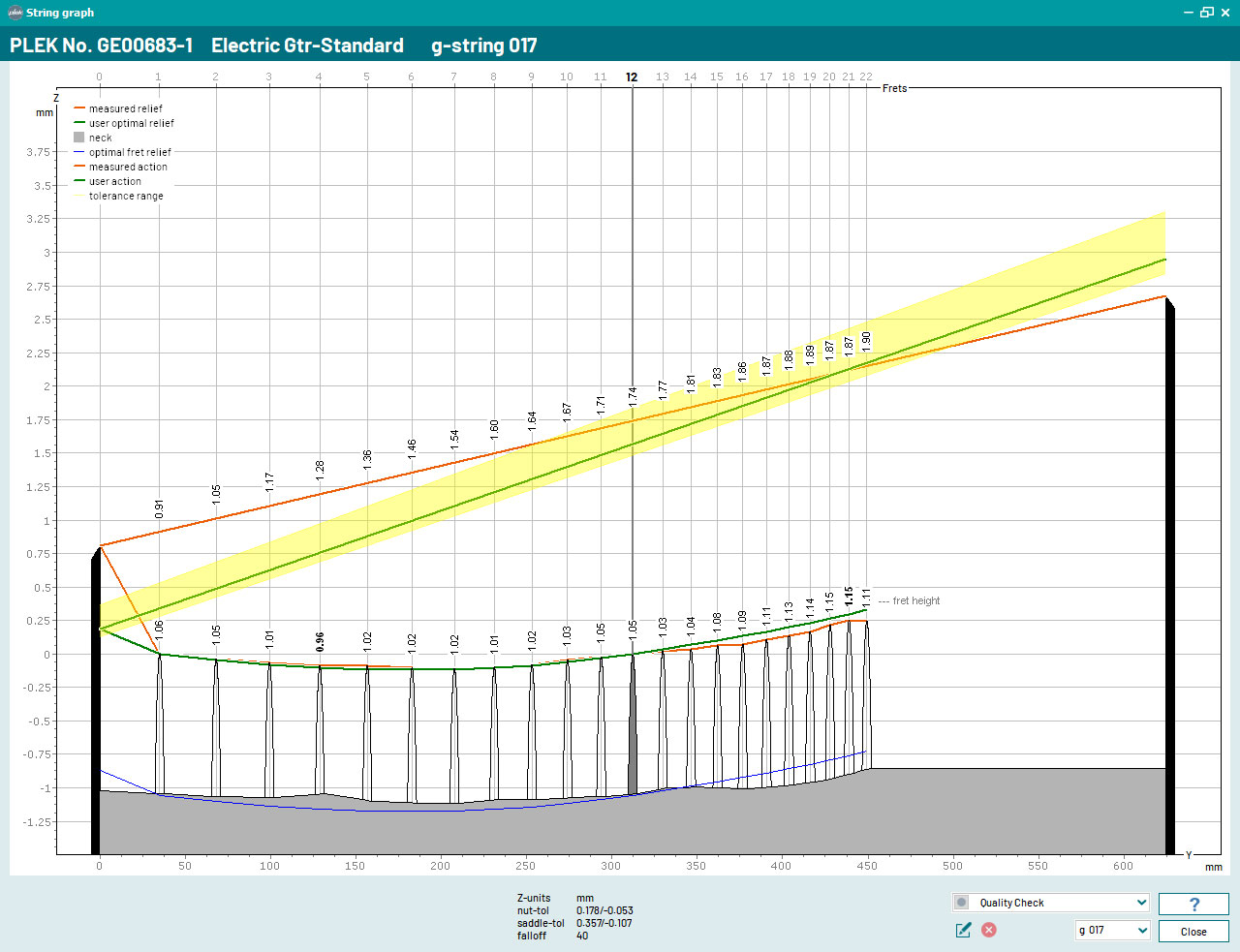
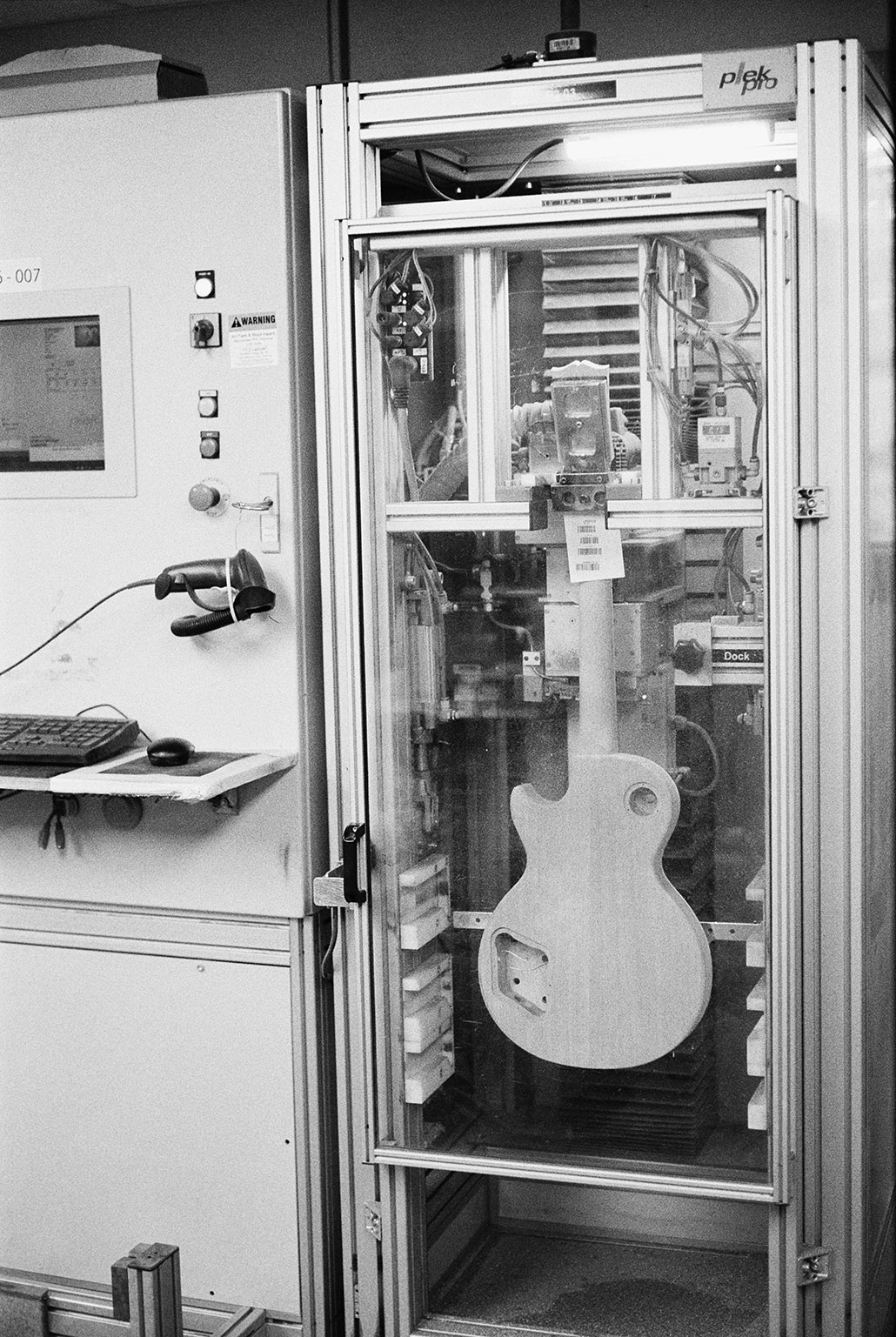
After the frets are dressed and finessed, PLEK then cuts the nut slots, taking into account the desired string spacing at the nut end, the ideal nut slot height in relation to the fret height, and the profile of the edges of the fingerboard. And, of course, PLEK also considers the desired string gauge, scale length, and neck curve. A skilled PLEK technician can work with the system to create a flawless setup for each guitar, working with the qualities of each instrument’s unique woods to create a more consistent feel from guitar to guitar despite their inherent differences. Note: Plek Pro may cut frets first and nut second, but Plek Station needs the nut cut first so the instrument can be strung up to tension.
When the guitar’s frets, nut, and saddle have been processed, the instrument is strung up and tuned. A final scan is undertaken to determine if the result corresponds to the set specs. PLEK leaves a fairly smooth fret surface behind, but a technician performs the final dress and polish.
The PLEK machine takes about 15 minutes to finish its task. It was initially introduced on the Gibson Custom Shop’s Les Pauls, graduating to SGs. Almost a decade later, PLEK is used across the Gibson line.
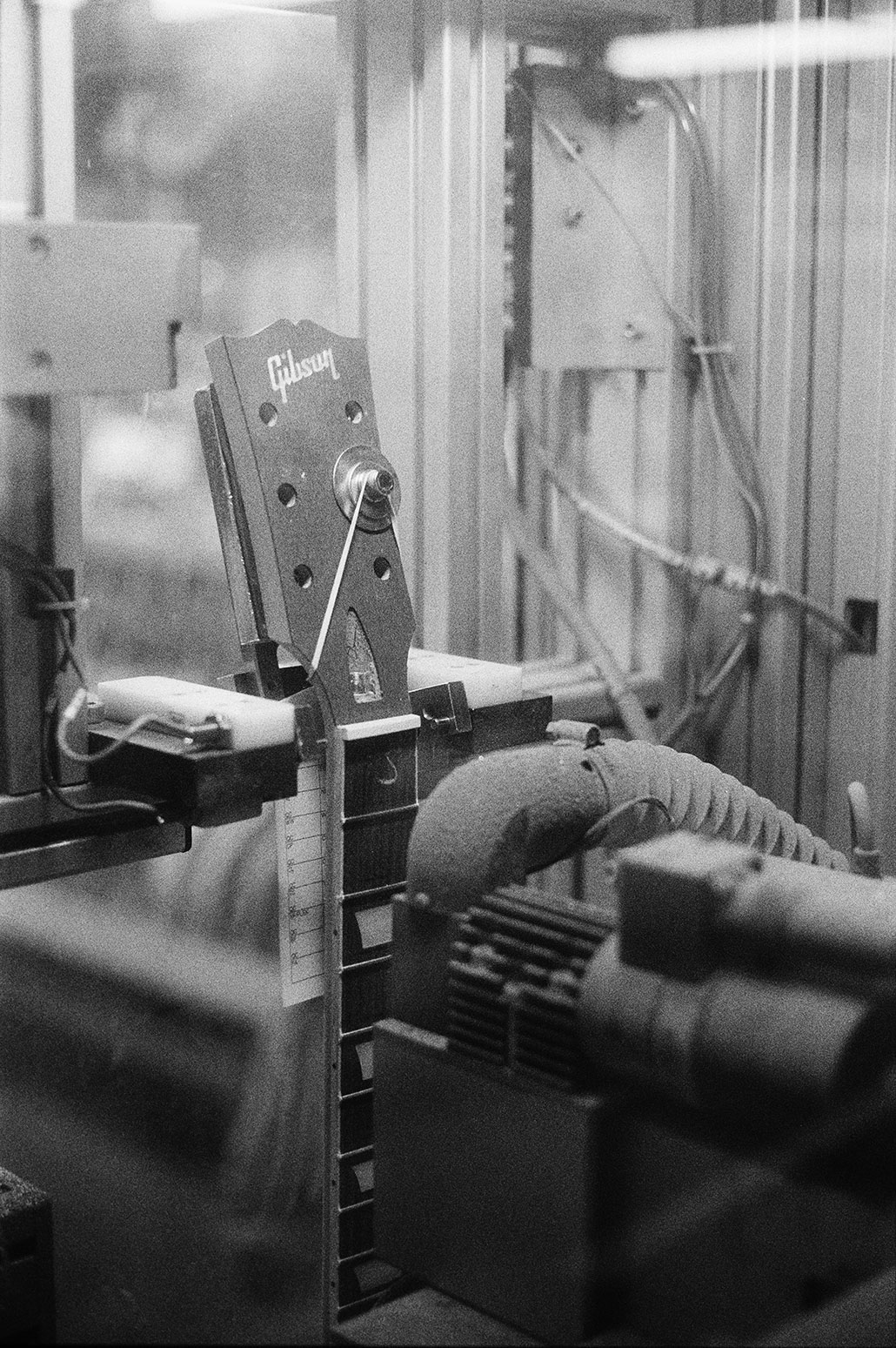
We talked to an expert, the professional bassist and Repair & Restoration Technician/Plek Operator, Kirk Eberhard.
Kirk relates this useful information to set the stage for our discussion:
The PLEK Pro machines used at our USA craftory are designed for new construction, performing a fret-leveling process when the instrument is in an unfinished (“white-wood”) state—without finish or hardware. The PLEK Station I operate differs from PLEK Pro because it is designed for scanning instruments under actual string tension. The PLEK Pro only simulates string tension, gripping unstrung instruments in its cradle in a manner that imparts relief on the fretboard to approximate being strung up. The obvious benefit of scanning with strings installed is that the neck behaves more like an instrument in a playable state, which, of course, it is. This distinction of using actual string tension affords a more precise outcome nearly every single time.
Because player preferences vary so much, what does PLEK bring to the table?
PLEK offers fine-tuning to a level that only the most skilled and experienced technicians can consistently bring to the fret leveling/setup process. PLEK scans the instrument while under string tension, providing an accurate view of the neck relief. Traditional fret leveling requires the tech to straighten the neck, remove the strings, and then relax the truss rod before leveling. This means there is a possibility that the neck may not return to the ideal relief after being strung up again. After PLEK scans the fingerboard and frets, it is up to the technician to facilitate the optimal setup based on individual player preferences. These parameters include string gauge, nut slot height, bridge saddle height, etc.
What can PLEK do more accurately than a human, and why?
PLEK scans the fingerboard’s surface with a precision of 1/1000th of a millimeter, which is finer than human hair. The scan provides a visual representation of the fret tops and fingerboard along the string paths, which the technician utilizes to make a “virtual fret cut” onscreen before any actual material is removed. No guesswork is involved, and PLEK removes fret material only where directed. PLEK can plane fingerboards, level frets, shape string nuts and cut nut slots, and mill acoustic bridge pin holes and saddle slots to a high degree of precision. It can even route fret markers and custom fingerboard inlay using common CNC file types. All these tasks are performed with a level of repeatability and precision associated with only the most experienced luthiers.
What do you think is the most common misconception about the PLEK process?
That PLEK applies a one-size-fits-all approach to fret leveling and nut cutting (collectively referred to as a “setup”). In fact, the setup depends on the PLEK operator’s skill and experience and is extremely customizable.
A secondary misconception is that PLEK can work miracles to overcome severe defects in frets, fingerboards, and/or neck materials, such as severe fret wear or severely bowed/warped fingerboards/necks. Some problems are beyond the scope of PLEK’s setup process and require hands-on repair before proceeding.
What’s next for PLEK? Is there a next-gen version of the machine on the horizon that can do even more than it can already?
The developers of PLEK, A+D Gitarrentechnologie GmbH, keep current with software/firmware updates, but the essential technology and hardware remain fundamentally the same since PLEK’s introduction in 1998. New software versions bring refinements and new features, enhancing performance and user options.
What’s the most difficult part of setting up a machine to PLEK a guitar?
Loading an instrument into PLEK is not actually difficult, but it does take a few reps for the steps to become ingrained. Some odd-shaped instruments, like the Explorer, Flying V, and Firebird, require a bit of creativity to mount in the machine.
What happens to the material removed from the frets? Is it recycled?
Frets are typically made of Nickel Silver (actually Nickel/Copper/Zinc) for Gibson instruments. These materials are all used in string manufacturing, so Gibson is able to recycle fret dust along with old/cutoff instrument strings.
Has the PLEK machine ever gone haywire on something nice?
No, operator error would be the only factor in that scenario. The instrument is placed on an adjustable and extremely sturdy cradle and then strapped in place with thin metal straps. It won’t move from this position if properly secured, keeping delicate parts away from the cutter, so we take great care to double and triple-check before operations begin. The PLEK software provides clear guidance and prompts throughout the process, along with an abundance of text and video tutorials.
Compare the typical amount of time spent doing a thorough fret job by hand versus PLEK. How do the results compare?
PLEK is significantly faster than a fret leveling performed by hand because the FCH (Fret Cutting Head) crowns the fret tops as it levels them—rarely is there any need to crown frets after PLEK completes the leveling phase. The cutter surface has three different cutting shapes machined in, so the radius and width of the crown can be tailored to the size of the fret wire and individual preference.
As a quality step, we occasionally check the handwork performed by our technicians by scanning the instrument in the PLEK machine. The accuracy of planing/fretting work done by our Repair & Restoration team is top-notch, and the visual scan in PLEK provides feedback that is extremely useful for both training and quality assurance purposes.
Shop All PLEK’d Gibson Electric Guitars and Acoustic Guitars
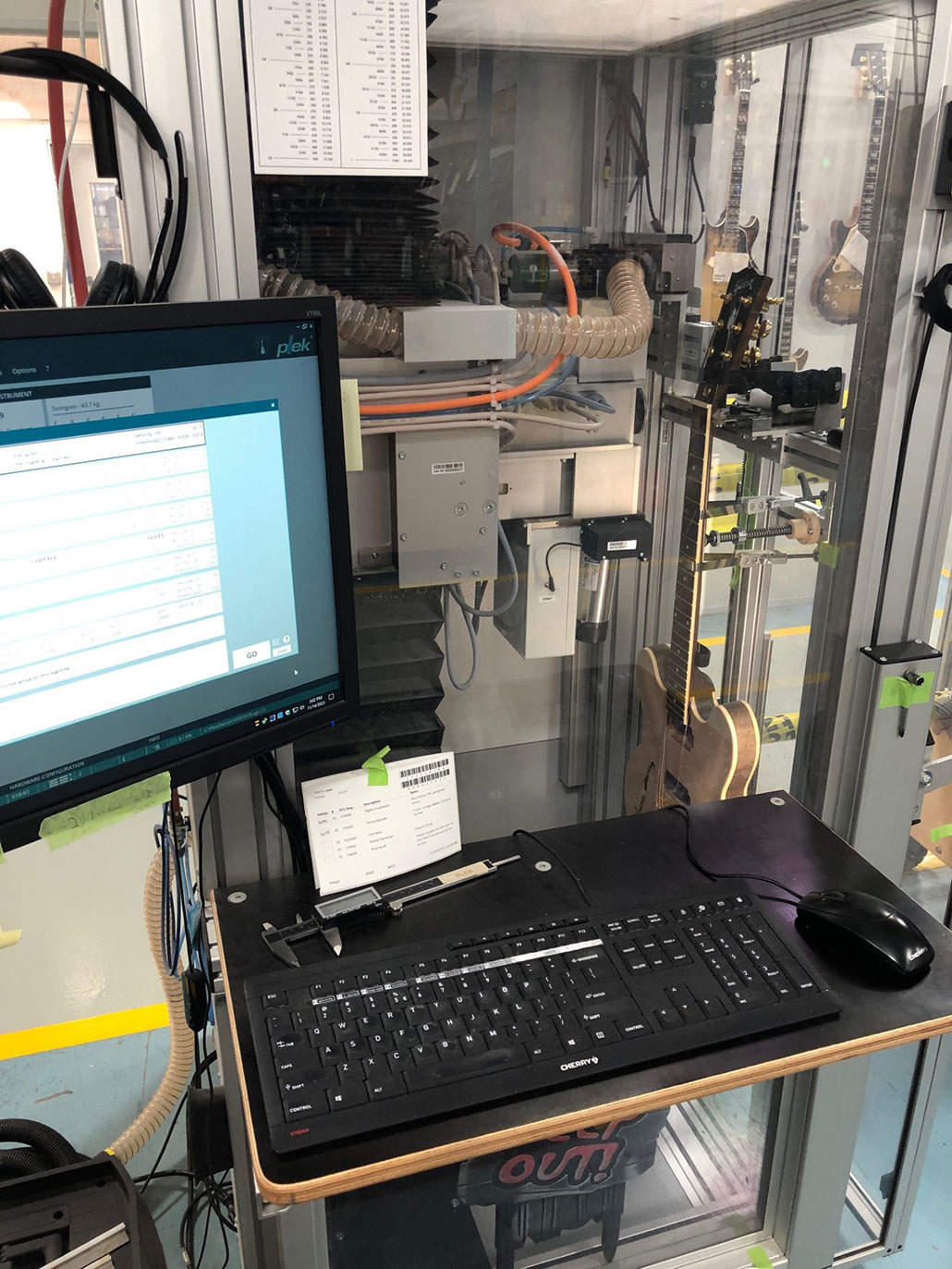
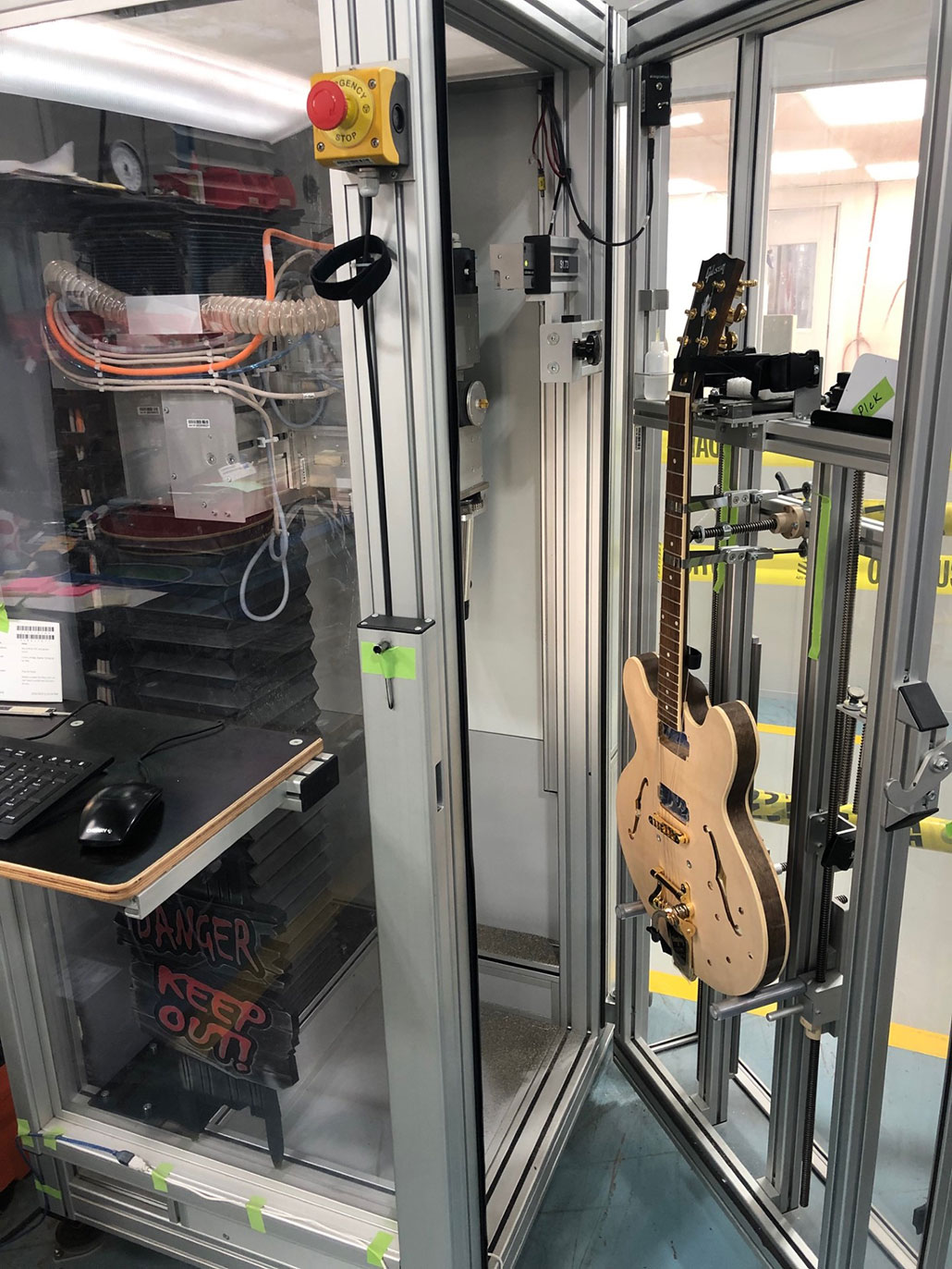
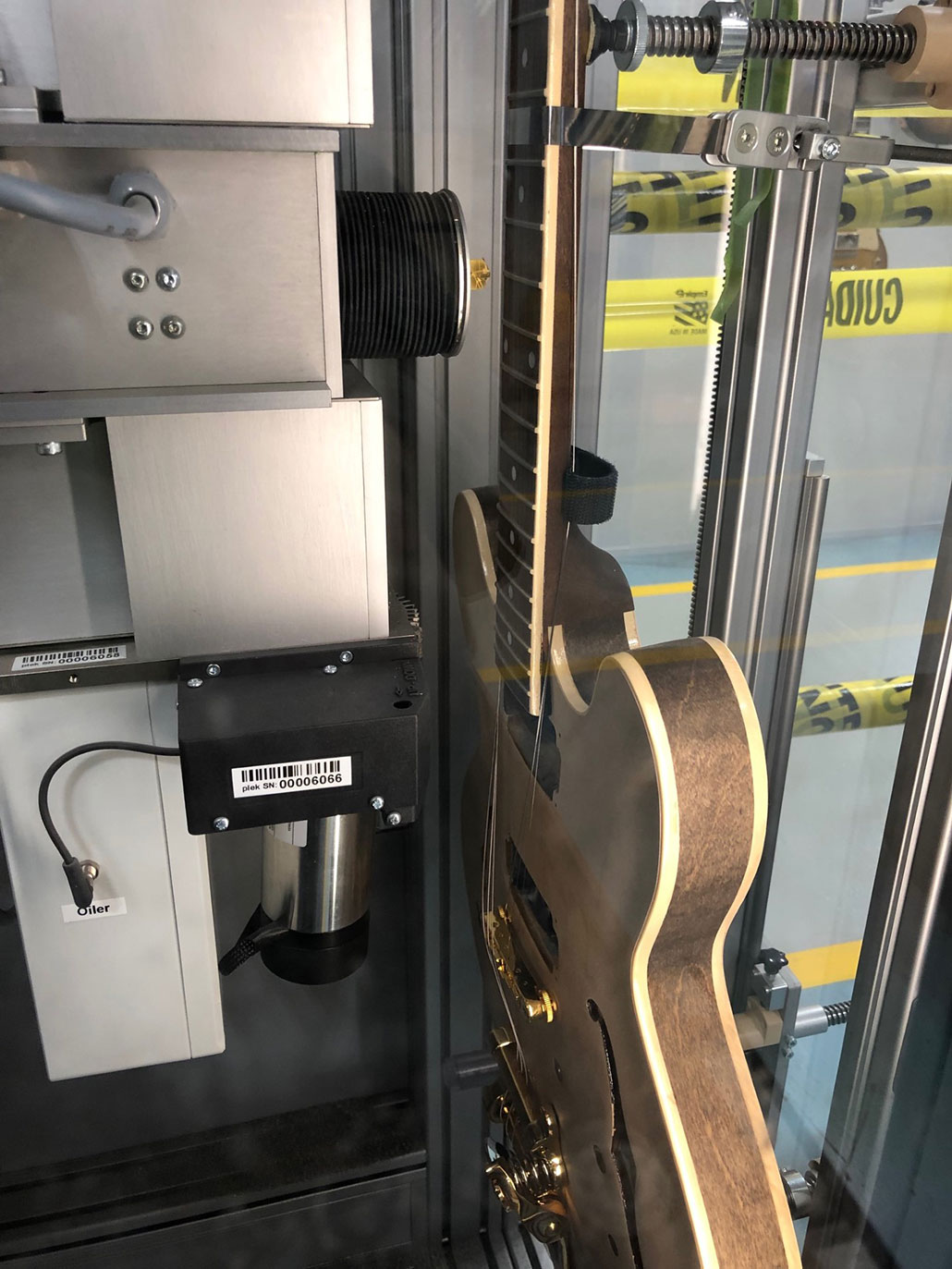

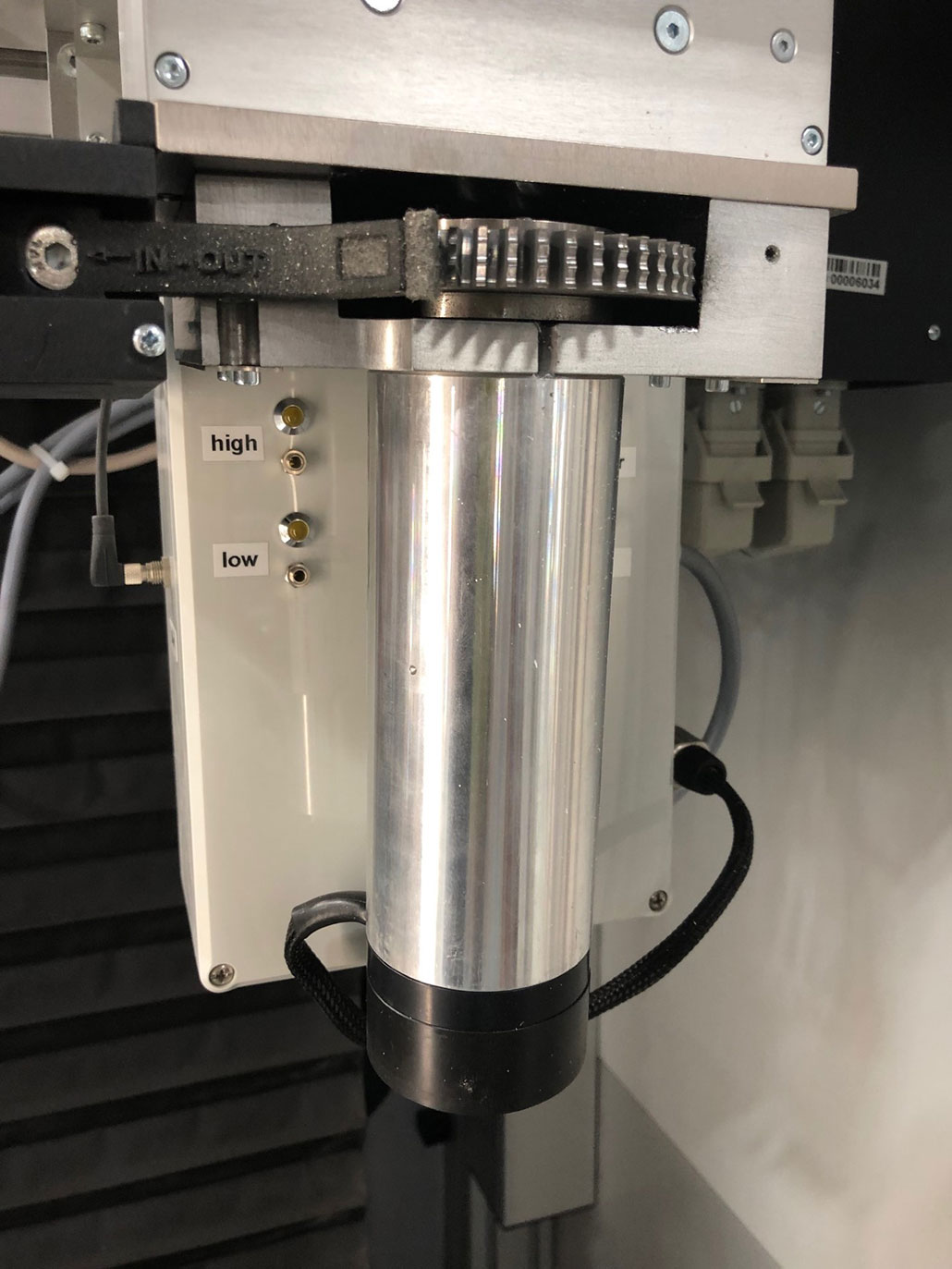